Since the beginning of humanity, humans have been adapting and innovating technology to create a better quality of life. From the steam engine to complex robotic assembly lines, humans have constantly pushed toward a more productive future. These technological advancements are marked in history as the Industrial Revolutions. The original industrial revolution refers to the time of momentous change from an agricultural economy to an industrial economy.
Since then, there have been three more “Industrial Revolutions” all with important technological advancements that launched humanity forward. Currently, there is debate on if we are in the midst of a Fifth Industrial Revolution. But to understand the Fifth Industrial Revolution also known as Industry 5.0, one must also understand the previous eras of development that heavily contributed to the creation of Industry 5.0.
The Industrial Revolutions
The first industrial revolution refers to the era of change in the 1700s from an agricultural and handicraft economy and society into the industrial and machine manufacturing-dominated society we know today. The Industrial Revolution started in Britain with the invention of the steam-powered engine which propelled industries into unprecedented productivity levels as factories went from relying on hand production to machines. It also revolutionized transportation, from steamboats to steam-powered trains. People (and their ideas), animals, and products were able to move farther and faster than ever before.

The Second Industrial Revolution was built on the engineering achievements of the First Industrial Revolution and many experts find an overlap of technology between the two eras. Mass production was in full swing with engineers and business owners looking for more innovative ways to make and sell as many products as possible. Technological advances such as electricity and the invention of the assembly line process skyrocketed factory efficiencies and productivity. The assembly line was the start of automation in manufacturing. Product prices dropped with the cost of labor, making more products, ranging from cars to clothing, more accessible to the average consumer. The Second Industrial Revolution ended with the beginning of World War I in 1914.
The Third Industrial Revolution is also known as the Digital Revolution and refers to the shift from analog to digital electronics. In manufacturing, the Third Industrial Revolution introduced programming for machines that allowed the further automation of the process with less even human interaction. The invention of the Personal Computer and the Internet laid the groundwork for our strong connectivity between devices. Advancements in computers and machines also meant data collection and analysis that led to data-driven decisions to increase factory production productivity.
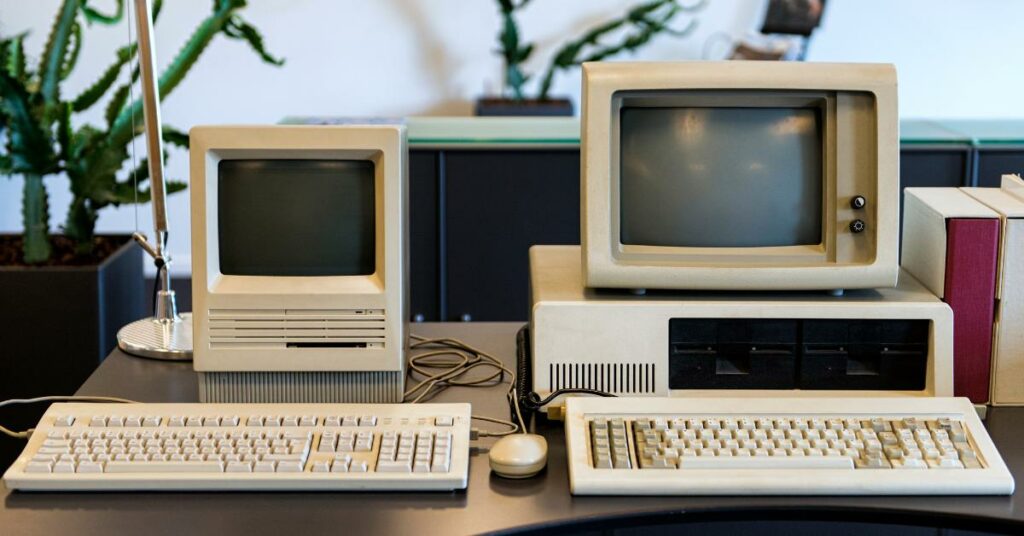
Industry 4.0
Industry 4.0 also known as the Fourth Industrial Revolution encapsulates the most recent era of technological advancements in manufacturing. Building off of the developments of the Digital Revolution, Industry 4.0 strives for total automation through advanced engineering, robotics, connectivity, and data analytics. The COVID-19 pandemic pushed many slow Industry 4.0 adopters to upgrade their systems and processes as companies were forced to adapt to supply chain issues, worker shortages, and increased consumer demand.
Many trends and new developments in Industry 4.0 contribute to the full automation of processes in a factory. Recent developments in robotics that made robots more accessible as they are cheaper to produce and to buy and integrate into production lines. Robots’ integrated sensors contribute to the increased accuracy and precision that allows more complex applications. The sensors are connected to a larger network that helps communicate and coordinate the rest of the automation system and technicians.
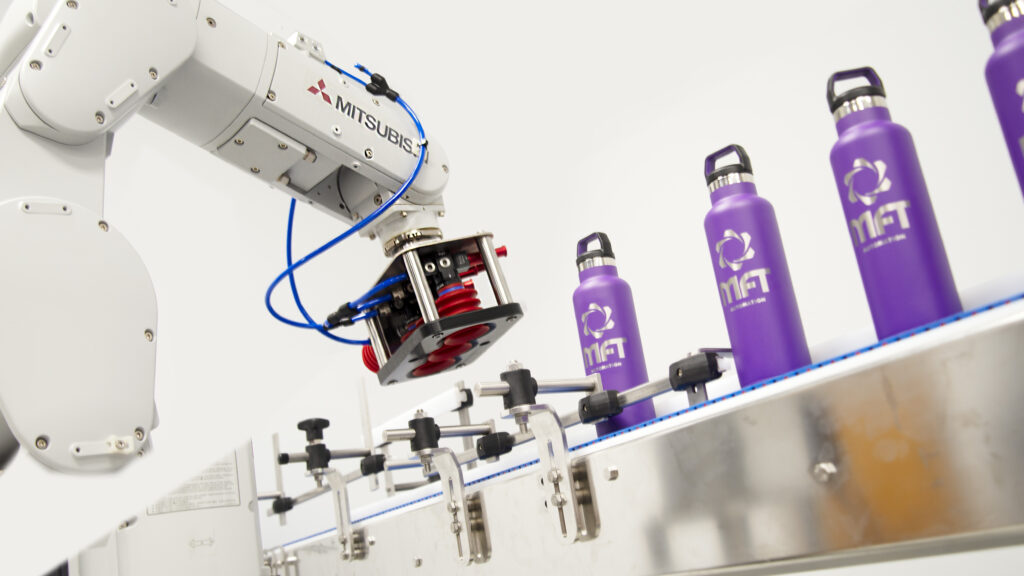
The productivity of an automation system is dependent on all the parts working together simultaneously and technicians who can stop a problem before it starts. Connecting all the moving parts of the system has never been easier. The Internet, bluetooth, cloud computing, and other wireless connections created a whole new level of connectivity, communication, and decentralized systems. Now, a network of machines, sensors, and other devices that communicate with computers over the internet creates an efficient automation system that technicians can observe and correct from anywhere.
IoT is not only used for communication but also for data collection. The data collected and analyzed gives powerful insights into the production lines to identify bottlenecks and other hazards impeding a production line’s full potential. Big Data is transforming companies and supply chains. From consumer data to production data all are brought together for companies to make better data-driven decisions. As technology evolves and the types of data that can be collected expands companies and stakeholders can expect to be more confident in their decisions.
On the horizon: Industry 5.0
Engineers are forward thinkers looking for the next thing so it is no surprise that some experts argue that Industry 4.0 is starting to become a thing of the past and Industry 5.0 is starting to take shape. Much like the overlap between the first and second industrial revolutions, Industry 5.0 builds on Industry 4.0. While Industry 4.0 focused on creating the most efficient and productive automated manufacturing process, Industry 5.0 looks to add a human element back into the process. Industry 5.0 looks to merge the potential accuracy of full automation and the problem-solving skills and creativity of human workers. The emerging trends of Industry 5.0 include Machine Assisted human collaboration, artificial intelligence, and sustainability.
Machine-Assisted Human Collaboration – Cobots
Human touch or the human element of manufacturing is much more difficult to eliminate than once thought. According to the International Federation of Robotics, only 10% of jobs will be fully automated. It is more likely that robots will work alongside human workers, the Robots being known as cobots. Cobots are not designed to replace the human workforce but to take over dull, repetitive, and dangerous tasks. The number of cobot installs doubled from 2017 to 2020 as the COVID-19 pandemic pushed companies to find ways to battle the worker shortage and social distancing measures.

Artificial Intelligence
The next Industry 5.0 evolution of data analytics is Artificial Intelligence (AI). Creating systems that combine human and machine intelligence. New advancements in Artificial Intelligence have been making headlines, from ChatGPT to Deepfakes, A.I. has become powerful enough to enter the mainstream. In manufacturing, A.I. is used to optimize and streamline production processes. Algorithms are able to analyze trends in data and forecast with higher accuracy. It was found that applying AI-driven forecasting to supply chain management reduced errors by 20%-50%. AI won’t completely replace humans in most functions as it still needs to be trained and often the analytical results still need human interpretation. AI is meant to help support humans, lessening human cognitive labor so humans can focus on more complex and creative problem-solving.
Sustainability
The conversation about climate change has led to more environmentally conscious consumers that are looking to support more sustainable companies. These companies are also becoming more aware of the finite nature of many resources and are looking for ways to make their company more sustainable in the long run. With governments, consumers, and now data pointing to the need for a more sustainable strategy, Industry 5.0 companies are taking responsibility and engaging in more sustainable practices to reduce or minimize their environmental damage. The goal is to be a net positive force in fighting climate change rather than stagnate or maintain the bare level of sustainability.

Your Industry 5.0 Partner
MFT Automation has over 25 years of experience in the Automation Industry as a leader in high-performance system solutions and integration. Our team features forward thinkers and innovators looking to help companies reach Industry 5.0. Our success is made possible by our engineering-oriented and customer-driven approach to finding the best automation solution for a customer’s application. With an expansive catalog of standard robust equipment that can easily be integrated into existing production lines or its own stand-alone solution. We focus on tailoring the solution to the application and not the other way around.
MFT Automation has an abundance of in-house resources that include Mechanical, Electrical, and Software engineers, and a machine shop with modern CNC and lathe machine tools. Our connections and partnerships allow for limitless opportunities and resources to create the perfect system. We work with customers from the first solution draft to integration to installation and training. Contact us with your latest labeling automation challenge, online or call us at 1-651-427-1255.