Medical Tyvek Pouches
Medical Tyvek Pouches
Tyvek is a lightweight, waterproof, and tear-resistant material used in the medical industry, most notably in medical packaging and personal protective equipment (PPE). Tyvek pouches are used in medical packaging as the fabric can withstand the gamma irradiation or ethylene oxide gas used to sterilize equipment and surgical devices. All medical device packaging must have some form of Unique Device Identification (UDI) such as barcodes, serial numbers, or other identification. UDI and Serialization are essential for the identification and tracing of incidents and defects. Printing on Tyvek is challenging as the material is water-resistant making it difficult to print with regular ink.
Thermal Transfer Print System
MFT Automation’s Thermal Transfer Print system combines our high-performance MFT Friction Feeders with a thermal transfer printer to create one powerful print system. The Thermal Transfer print engine is the best option for printing on Tyvek. Thermal transfer printing is when a material is applied to paper by melting a coating ribbon that glues the ink to the material. Thermal printing lasts longer as it is not water-based ink and is dried to the surface. Other ink printers would have problems with Tyveks’ water-resistant properties and the inks do not dry in time before continuing on to the next step of the process.
To accommodate the strict sanitation standards of the medical device packaging industry, the system can be outfitted with Hygienic Washdown equipment that is specifically designed for environments that need to be kept sanitary. Made with Type 304 Stainless Steel, the material of choice for medical packaging applications, the equipment is designed to be repetitively and aggressively cleaned every day to adhere to safety regulations and guidelines.
See the system in action:
MFT Automation
MFT Automation has been helping customers design, build, and integrate high-performance automation solutions for over 25 years. MFT Automation’s equipment, systems, and services are known for their flexibility, accuracy, and performance. Our success is made possible by our engineering-oriented and customer-driven approach to finding the best possible automation solution for customers’ applications. With an abundance of in-house resources including Mechanical Engineering, Electrical Engineering, Software Engineering, and a machine shop with modern CNC and lathe machine tools, we work with customers from the first solution draft to installation and integration. Contact us with your latest automation challenge, online or call us at 1-651-407-3100.
Want to See How your Product Integrated
with our Machines?
Send us a sample and we will make a demo video showing how your products feed through our machines.
Feeding and Folding
Feeding and Folding
Folding papers is a slow and tedious task with varying quality depending on the person folding the papers. It is easy to automate folding tasks with consistent and high-quality results. Folding assemblies are compact and simple in design, lending them to integrate into systems and existing production lines easily. There are two types of automated folding techniques, each with its own folding assembly equipment and setup.
Plow Folding
Plow Folding is used when folding from the side, or book-style folds. It uses a sturdy, curved metal plate and a roller to fold and crease the product. In a matter of seconds, a product moves down a conveyor and the curved metal plate guides it to a folded position for the roller to crease. The small size of the metal plate allows for easy integration into systems and existing production lines. Plow folding is the most efficient high speed folding technique that maintains accuracy while folding. Plow folding is recommended for applications such as applying wafer seals to booklets/magazines, tamper evident seals to electronics packaging, carton or box folding, creating pamphlets, and any other application where folding along the side edge of a product is required.
Buckle Folding
The buckle folding method folds from front to back. It uses high speed and force to fold products. The product moves rapidly down a conveyor and then the lead edge is driven into a buckle plate, which is a rigid sleeve that is close to the product thickness.
The buckle plate has a backstop, and when the lead edge of the product hits the backstop the product is forced to “buckle” near the entrance of the buckle plate. Just downstream of the buckle plate opening is a folding roller (or rollers) that grabs the product where the buckle fold begins to form. The folding roller forces the lead portion of the product that was captured by the buckle plate to fold over backwards as the product is driven through the roller, creasing the fold in the process. This process is slower than plow folding but is required to create a front-to-back fold. Buckle folding is recommend ed for applications such as creating booklets, folded inserts, magazines, carton folding, and any other application where front-to-back folding is required.
MFT Friction Feeders
Friction feeders are efficient automation equipment that separates and dispenses flat products from a vertical stack, one product at a time. Paper or cardstock is a standard product fed through friction feeders. With a diverse selection of friction feeders ranging in sizes, maximum speeds, sanitary requirements, and more, MFT Automation has a high-performance friction feeder that will fit your application. MFT Automation offers four friction feeder families: Signature Series (v3), Industrial Performance Series (ip3), High Continuous Performance (HCP) Series, Hygienic and Washdown series. Our v3 series is our economical and cost-efficient feeding solution, engineered for lower throughput and low-speed applications. Our Ip3 Series is our classic premium friction feeding solution, designed for industrial environments. The HCP Series features hard carcass belts that can withstand high-speed applications. Our Hygienic and Washdown series is specifically designed for end customers in the food, medical, and pharmaceutical industries that need to repetitively and aggressively clean their production floor equipment. All MFT friction feeders have a compact design making them easy to integrate into existing production lines. With powerful software and robust parts, MFT friction feeders are built for long runs and years of quality service.
MFT Automation has been helping customers design, build, and integrate high-performance automation solutions for over 25 years. MFT Automation’s equipment, systems, and services are known for their flexibility, accuracy, and performance. Made possible by our engineering-oriented and customer-driven approach to finding the best possible automation solution for customers’ applications. With an abundance of in-house resources including Mechanical Engineering, Electrical Engineering, Software Engineering, and a machine shop with modern CNC and lathe machine tools, we work with customers from the first solution draft to installation and integration. Contact us with your latest automation challenge, online or call us at 1-651-407-3100.
Want to See How your Product Integrated
with our Machines?
Send us a sample and we will make a demo video showing how your products feed through our machines.
Feeding Tyvek Envelopes
Tyvek Envelopes
Tyvek is a moisture, rip, tear, and puncture-resistant paper-like material, making it the perfect material for envelopes. Commercial mailing envelopes need to withstand mail sorting machines that operate at high speeds and often snag or jam, leading to damaged mail. The envelopes also have to survive the elements and rough handling by postal workers. Made from high-density polyethylene fibers, the moisture, and tear-resistant material allows for peace of mind when sending important materials through the mail. The same qualities that make it great for commercial mailing also lend Tyvek envelopes to document storage and protection applications. Tyvek is the perfect archival material, as it is pH-neutral, moisture-resistant, and tear-proof. Automating the handling of Tyvek envelopes is easy with the right equipment.
MFT Friction Feeders
MFT Automation offers a wide range of Friction Feeders to fit your automation needs. Friction feeders are a powerful piece of automation equipment that separates and dispenses flat products from a vertical stack, one product at a time. They are ideal for automatically feeding the flat Tyvek envelopes into an automation system. From larger sizes to fit your oversized envelopes to high-speed options to fit the pace of your production, an MFT Friction Feeder will fit your application.
Industrial Performance Series
The Industrial Performance (ip3) Series is MFT Automation’s classic premium feeding solution. With multiple sizes to fit the size of your application, the standard features of an MFT ip3 make it perfect for feeding Tyvek Envelopes. All ip3 feeders have proprietary stripping wheels that come in different widths and materials to fit the product. different gearing options that aid in product separation during the transfer from the infeed to the discharge, providing ease of use and versatility in product feeding. The Double Detect Sensor guarantees a correct count with accurate overlap detection. Powered by a 750-watt (optional 1000-watt available) brushless servo motor, the ip3 Series is built to provide years of uninterrupted service.
High Continuous Performance Series
The High Continuous Performance (HCP) Series is MFT Automation’s next level of friction feeding, expanding on the performance and accuracy already built into the MFT ip3 Series. The HCP series has the standard features of the ip3 Series and upgrades the belts to premium high-strength hard carcass belts that have minimal stretch for longer and faster production runs. Vacuum belts are also available which allow for tighter control and an open face for applications such as track and trace and quality control where the product needs to be exposed. The HCP series unifies high-performance parts with specially tuned software for high linear speeds and tighter placement which equates to more product throughput.
Necessary Accessory: Static Bar
MFT Automation also has an extensive assortment of components and accessories to customize and tailor your friction feeder for the job. Our most common accessory for Tyvek feeding is the static bar to reduce the static often associated with the Tyvek material. Friction associated with the feeding process can impart static onto products as they are separated and dispensed. Static causes the envelopes to stick together and cause overlaps, jams, and quality issues. The static bar dissipates the static charge as the products exit the friction feeder discharge.
MFT Automation
MFT Automation has been helping customers design, build, and integrate high-performance automation solutions for over 25 years. MFT Automation’s equipment, systems, and services are known for their flexibility, accuracy, and performance. Our success is made possible by our engineering-oriented and customer-driven approach to finding the best possible automation solution for customers’ applications. With an abundance of in-house resources including Mechanical Engineering, Electrical Engineering, Software Engineering, and a machine shop with modern CNC and lathe machine tools, we work with customers from the first solution draft to installation and integration. Contact us with your latest automation challenge, online or call us at 1-651-407-3100.
Want to See How your Product Integrated
with our Machines?
Send us a sample and we will make a demo video showing how your products feed through our machines.
Integrated Systems for Coffee Bag Production Lines
High-Performance Packaging and Labeling for Coffee Bags
The pandemic has driven many consumers to start brewing their own coffee with work from home and price surges. Coffee bags and their labels help brands stand out on the shelves and communicate important things to customers, such as the coffee’s taste, ingredients, and more. For a growing business, labeling by hand might become too overwhelming as orders grow. Automating the labeling process has its challenges. Some coffee bags are made of slippery materials or have resealable parts that stick outside the edge of the bag. These factors make the coffee bags hard to handle for many automated systems. But with the right system, automating your coffee bag labeling process is easy.
MFT Automation’s Impresso Labeler and Friction Feeder for Coffee Production
The Impresso Labeler and Friction Feeder System combine our robust friction feeder with our highly accurate and precise labeler. The friction feeder dispenses the product onto a short conveyor where it is brought to the labeler to be efficiently labeled. The friction feeder can be customized for your coffee bags to fit and easily be fed through the system. The Impresso consistently labels the bags with accuracy and precision. This compact system easily integrates into any existing production line with its modular and customizable design. The comprehensive software package features overlap detection to ensure an accurate count of products. Not only is the Impresso Labeler and Friction Feeder System highly efficient and effective, but is also remarkably easy and versatile to interface using standard industry-compliant connectors.
MFT Automation
MFT Automation has been helping customers design, build, and integrate high-performance automation solutions for over 25 years. MFT Automation’s equipment, systems, and services are known for their flexibility, accuracy, and performance. Our success is made possible by our engineering-oriented and customer-driven approach to finding the best possible automation solution for customers’ applications. With an abundance of in-house resources including Mechanical Engineering, Electrical Engineering, Software Engineering, and a machine shop with modern CNC and lathe machine tools, we work with customers from the first solution draft to installation and integration. Contact us with your latest automation challenge, online or call us at 1-651-407-3100
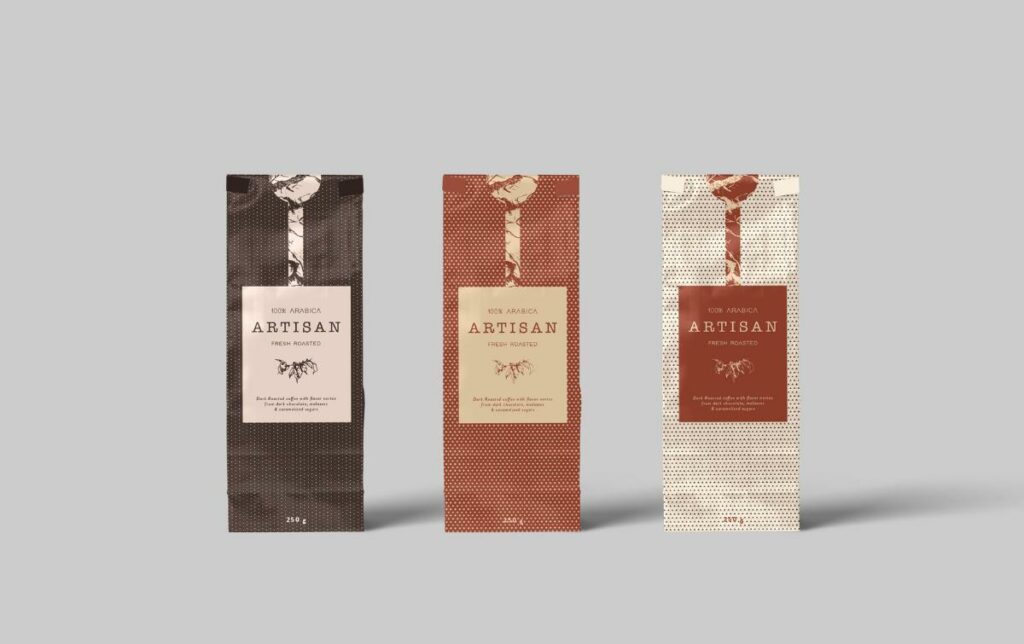
Want to See How your Product Integrated
with our Machines?
Send us a sample and we will make a demo video showing how your products feed through our machines.
Bandages
Bandages
Bandages, from small band-aids to gauze, often require a sterile packaging environment. Keeping the bandages safe and sterile is vital due to their usage to treat open wounds. Decreasing the risk of contamination is a top priority. Most companies have turned to automation to decrease the amount of human contact and reduce the risk of contamination in the necessary sterile environments. The most common application when packaging bandages is feeding batches of bandages into boxes. Do you have the right equipment to package your products safely?
Hygienic Washdown Friction Feeders
MFT Automation’s Hygienic Washdown series meets sanitary requirements and complies with IP66 or higher as well as NEMA4X standards. The hygienic friction feeder is designed for end customers in industries that need to repetitively and aggressively clean their production floor equipment.
This clean-in-place (CIP) friction feeder is engineered with type 304 stainless steel which is moisture and corrosion resistant to meet FDA standards. The open design allows for minimal disassembly for easy cleaning and maintenance. This machine is self-draining and has compatible materials with no hollow areas, which is a principle we follow to ensure a sanitary design and reduced risk of contamination.
MFT Automation has been helping customers design, build, and integrate high-performance automation solutions for over 25 years. MFT Automation’s equipment, systems, and services are known for their flexibility, accuracy, and performance. Made possible by our engineering-oriented and customer-driven approach to finding the best possible automation solution for customers’ applications. With an abundance of in-house resources including Mechanical Engineering, Electrical Engineering, Software Engineering, and a machine shop with modern CNC and lathe machine tools, we work with customers from the first solution draft to installation and integration. Contact us with your latest automation challenge, online or give us a call at 1-651-407-3100.
Want to See How your Product Integrated
with our Machines?
Send us a sample and we will make a demo video showing how your products feed through our machines.
Bubble Mailers
Bubble Mailers or padded envelopes are commonly used to ship flat, fragile, or smaller objects that are too big for envelopes but too small for boxes. Items such as CDs, jewelry, books, DVDs, and more can safely be shipped in bubble mailers with lower shipping fees. Labeling bubble mailers can be a bottleneck in the packaging and shipping process. The quality of manual label placement also suffers as workers are overloaded with demand. Automating the printing and labeling process can increase output and quality. Automated labelers are faster and label placement is much more precise and accurate compared to manual placement.
150 Print and Apply
MFT Automation’s Print and Apply labeling systems prints and adheres labels to bubble mailers with ease. The system has a modular design with the ability to use different print engines, allowing for print quality customization. Customization allows matching the printing engine to a customer’s existing print engine so there is no learning curve in maintenance for a new print engine. The labeling system features the MFT Automation Smart Pad, an applicator that automatically adjusts to the product’s height and places labels accurately and reliably. The MFT Automation Smart Pad is easy to changeover to customize for different size labels and does not necessitate tools.
MFT Automation has been helping customers design, build, and integrate high-performacne automation solutions for over 25 years. MFT Automation’s equipment, systems, and services are known for their flexibility, accuracy, and performance, made possible by our engineering-oriented and customer-driven approach to finding the best possible automation solution for customers’ applications. With an abundance of in-house resources including Mechanical Engineering, Electrical Engineering, Software Engineering, and a machine shop with modern CNC and lathe machine tools, we work with customers from the first solution draft to installation and integration. Contact us with your latest automation challenge, online or give us a call at 1-651-407-3100.
Want to See How your Product Integrated
with our Machines?
Send us a sample and we will make a demo video showing how your products feed through our machines.
Currency
Currency Production & Packaging
In the United States of America, as of December 31, 2020, there was $2,040.7 billion in circulation, totaling 50.3 billion notes in volume. Every year the Federal Reserve puts in an order for new notes. More than 70% of notes in the Federal print order will be used to replace notes considered unfit for circulation. As the saying goes, money doesn’t grow on trees. In fact, the U.S. Bureau of Engraving and Printing in Washington, D.C. which prints the currency runs 24 hours a day. After the currency is printed and cut it must be stamped to be officially issued by the government. Now that the notes are official, they must be distributed to the public. Notes are counted and banded together for distribution. They are then given to the Federal Reserve bank which will distribute the legal banknotes to the public through commercial banks, credit unions, and savings and loans associations.
Batch, Count, and Band System
Enhance your currency production and packaging process with the Batch, Count, and Band System. Utilizing MFT Automation’s robust Friction Feeder, Automatic Product Loader (APL), and Shingling Conveyor the Batch, Count, and Band System increases the productivity and accuracy of the banknote production and packaging processes. MFT Automation’s powerful ip3 Series of Friction Feeders accurately count products at high speeds. The APL maximizes run times between product reloads by expanding the friction feeders’ capacity. Once a pre-set count of products has been accumulated, the pneumatic pusher securely delivers the stack of products to the bander, where the band is applied and the finished product is offloaded onto the shingling conveyor for operator removal. Our automation experts are available to help develop similar systems to meet a customer’s specific needs.
With over 25 years of experience in the industrial automation industry, MFT Automation is here to help solve your automation challenges. For further information on how to automate your currency production and packaging process, give us a call at 1-651-407-3100 or contact us online.
Want to See How your Product Integrated
with our Machines?
Send us a sample and we will make a demo video showing how your products feed through our machines.
Blister Packs
Friction Feeder For Blister Packs
Blister packs are a type of pre-formed packaging that has a cavity or pocket made from plastic or foil that holds the product. The backing is usually made out of aluminum foil or plastic to seal the product into the cavity. The backing provides a tamper-evident seal as well as protects the products from humidity and contamination.
Commonly used in the pharmaceutical industry, blister packs are favored for being a cost-effective and tamper-evident way to package pills while effectively guiding the consumer to take the correct medication dose at the right time.
Most of the “blisters” in a blister pack contain a singular pill for an easy visual of the dosage amounts. The foil backing is durable but will show clear signs of tampering which is a strict requirement for safety in the pharmaceutical industry. The surface foil allows for smooth printing.
Time of day or dates can be printed on the foil backing to directly communicate when the medications should be taken as well as lot numbers and barcodes for verification and security.
Friction Feeders
MFT Automation offers a versatile catalog of robust, high-performance friction feeders that can increase productivity in your blister pack packaging process. The friction feeder’s flexible belts grip the blister packs without breaking the blister cavity or damaging its contents. The thickness of an average blister pack limits the stack height and therefore the capacity of the friction feeder. MFT Automation’s Automatic Product Loader (APL) expands the friction feeder’s capacity. The products are shingled on the APL and then a sensor mounted above the feeder’s infeed triggers the APL to top off the stack as it is depleted.
From counting and batching to printing applications to tipping into boxes, our friction feeders are modular in design to easily integrate into any existing production lines. With a wide range of sizes and discharge lengths to match your product, we work with you to find a feeder to fit your packaging application. MFT Automation also offers hygienic and washdown options to fit the needs and requirements of your environment.
Contact us today to discuss your application further. With over 25 years of experience in the packaging industry, MFT Automation has the tools and resources to personally find the best solution for your automation challenge. Call 1-651-407-3100 or contact us online.
Want to See How your Product Integrated
with our Machines?
Send us a sample and we will make a demo video showing how your products feed through our machines.
Automated Meat Soaker Pad Placement
Automated Systems for Sanitary Meat Production and Packaging
Meat soaker pads are a meat packaging industry standard. Used to soak up excess liquids from the raw meat, the flat pads can be made from a variety of absorptive materials, including silica gel or cellulose fibers. The meat juices can contain harmful bacteria that contaminate food preparation areas as the juices leak, spill, or drip out of the packaging.
The sponge-like material of the pads soak up and contain excess moisture, greatly reducing the likelihood of foodborne illnesses. Meat soaker pads are commonly tipped into the packaging tray by a friction feeder before the raw meat is packaged into the container.
Sanitary, Efficient, and High-Performance Washdown Systems
As the meat soaker pads have direct contact with the raw meat, it is recommended to use a Hygienic Washdown friction feeder to feed and tip the meat soaker pads.
The Clean-In-Place (CIP) design allows minimal disassembly for easy and convenient cleaning and maintenance. Specifically designed for the food industry and other sanitary environments, the Hygienic Washdown Friction Feeder series meets the sanitary requirements and complies with IP66 or higher as well as NEMA4X standards.
Made with type 304 stainless steel, Hygienic Washdown Friction Feeders are moisture and corrosion resistant, meeting FDA standards. The Hygienic Washdown Friction Feeder is part of a full line of Hygienic Washdown equipment and can be part of a full Hygienic Washdown system or be easily integrated into existing production lines.
Accutipping
In a tipping application, a friction feeder accurately places a flat tip-on product onto another product moving underneath the feeder (usually on a conveyor). When not automated, hand placing products can be slow with inaccurate and unrepeatable results. Accutipping is MFT Automation’s proprietary tipping software specifically engineered and tailored to MFT friction feeders.
The Accutipping Software makes micro-adjustments to the speed of the products during the feeding cycle to consistently match the spacing of the base products for precise and accurate placement. These reactive adjustments allow for high accuracy placements while maintaining fluidity and high speeds. Unlike other tipping software, Accutipping software has fine-tuning capabilities, and various debounce parameters are also available for flexibility.
With over 25 years of experience in the automation and packaging industry, MFT Automation is here to help solve your automation challenges. For further information relating to your food packaging needs, give us a call at 1-651-407-3100 or contact us online.
Want to See How your Product Integrated
with our Machines?
Send us a sample and we will make a demo video showing how your products feed through our machines.